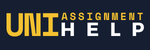
ENEM20002 Fluid Power Engineering and Control Report Sample
Essential sections of Project 2 are:
Produce a functional prototype (See note below) of you project following your design produced in Project 1;Produce simulated fluid (pneumatic or hydraulic including PLCs if required) control system for your selected machine (as in Project 1), then build the fluid (Pneumatic/hydraulic) control system and demonstrate functionality of you machine.
NOTE: In the current situation, for Project 2, prototype is replaced by design layout/assembly drawing (2D/3D) in side view/s and top view, visualise it and get clear understanding of your projected machine, you may need to produce part drawings of the selected parts of your machine (selection can be done by your Tutor).
Project 2 report content:
1) Title page.
2) Introduction and Background (improved version).
3) More confirmed CAD drawings (layout/assembly drawing, part drawings).
4) Fluid/Pneumatic control circuit integrated with PLC with proven functionality in respect of simulation and by performances of the built prototype.
5) For PLC programming use CX-programmer for OMRON PLCs, use Ladder Diagram method of programming. Submit hand written pneumatic circuit and PLC ladder program using CX-programmer (OMRON) along with computerised versions.
6) Demonstration of design improvement (in respect existing one, if any)
7) Cost estimation of the machine of your project.
8) Industrial applications and value of your projected machine for engineering and technology.
9) Safety factors that to be considered for operation of the projected machine.
10) List of references.
Produce a Report in group and present it together in group sharing sections of presentation in Week 12 using a PowerPoint file in the Workshop class. Presentation time 10 mins and another 5 mins for question and answer.
Solution
Introduction
The aim of the Fluid Mixing Plant project is to design and develop a efficient and low cost blending system for various applications in the food and beverage, wastewater treatment, chemical and pharmaceutical industries, and other fields where accurate measurement of two is critical for production of end products and processes. Normal mixing styles often yield inconsistent outcomes because they are imprecise and utilize excessive amounts of energy. Collectively, these components involve the integration of programmable logic controllers (PLCs), hydraulic control circuits to ease the control of the mixing process while enhancing its efficiency. It is also important to note that the main goal of the project is not only to design and simulate a high-performance system but to create a scalable, energy-efficient system that can accommodate the needs of contemporary industrial processes.
1.1 Problem Statement
Many problems have been found in traditional stirring systems, including low accuracy, low performance, and fluctuation of product quality. This is due to the fact that the commonly available mechanical mixers and agitators do not ensure homogeneous blending of the ingredients and often lead to variations in the composition as well as quality of the end product. These conventional systems also consume too much energy, hence affecting the environment and in the long-run, increase operating costs.
These applications for university assignment help require efficient mixing systems that can effectively manage different viscosity, temperature, and chemical interactions. These are areas that typical mixing systems cannot meet, leading to substandard performance and reduced viability in industries where fluid is a critical factor. It is intended to increase the capacity of the fluid mixing plant by developing a rigid, modular, power-saving, and flexible mixing system which can overcome all the limitations of conventional methods and give high quality product.
1.2 Objectives
The objectives of the fluid mixing plant project are as follows:
1. Design and develop a fluid mixing plant incorporating advanced fluid power systems.
2. Optimize the mixing process parameters, including fluid flow rates, pressures, and temperature control.
3. Develop an intelligent control system using programmable logic controllers (PLCs) to enhance automation, precision, and adaptability of the mixing process.
2. Previous Work and Research in Fluid Mixing System
Technology is a dynamic entity in field of designs of fluid mixing systems and appreciable improvements have been experienced due to emerging demand for achievability, productivity and versatility in a variety of applications in the industries. This paper presents a literature review of the more recent works and pioneering research conducted on and concerning the fluid mixing systems category of technology.
Mechanical mixers and agitators were traditionally the only means of fluid mixing widely used in the production industries including pharmaceutical, chemical, food and beverages, and wastewater industries. Conventional stirring devices such as paddles, impellers, and turbines has well been deployed because of its simplicity and reliability (fpt. , 2023). Then again, some of these systems are inconsequential with low precision, low productivity, and variably quality products. Some of the drawbacks of these systems have been established to cause non-uniform blending hence bringing in variation in the quality of the product been produced. Third, they often require higher amounts of energy and operating costs yet they exert major influences on the environment (iqsdirectory, 2022).
More recently, the use of computational fluid dynamics or CFD has made a great impact in the designing and modeling of fluid mixer systems. Pertaining to the CFD simulations, they enable the observers to envision the fluid flow distribution, mixing period and energy utilization. Different designs of impellers, shapes and sizes of the tank, and also operating conditions have been expressed analysis using CFD to determine the impact on the mixing process (Ian & Ji Changying, 2018). For example, the impellers that are used in mixers have seen changes in their design over the years through the use of hydrofoil impellers and the helical ribbon mixers, and CFD analysis has been used to enhance the efficiency of mixing and energy recovery (Aubin & Xuereb, 2006).
Intelligent control systems, especially involving PLC’s (Programmable Logic Controllers) are one of the most progressive advancements of fluid mixing technology. PLCs also allow control of the mixing parameters to be fine-tuned and adjusted as necessary, with a high degree of process control that would facilitate operations in real time (Scully, 2024). There is evidence that reviewing and implementing basic operating procedures that include the proper functioning of PLCs helps enhance quality in the mixing process and also reduce energy consumption. For instance, a change incorporated the use of PLC to control the mix procedure in the production of Pharmaceuticals, which guarantees the incorporation of active ingredients into position all through the mixture (Bowler et al. , 2020).
The effects if the shortcomings of these methods of mixing have however led to the development of other advanced methods of mixing. One such technique is ultrasonic mixing, which utilizes sound frequencies to create pressure variations in the liquid that lead to the creation of microscopic bubbles which expand and contract rapidly; thereby promoting rapid mixing at the molecular level according to Hoo et al (2022). Ultrasonic mixing has been used in the organization of nanoparticles and emulsion of phase-separated immiscible liquids, and it is helpful in applications such as in drug delivery and food processing as explained by Singla and Sit (2021). Another technique is magnetic mixing which enhances the use of magnetic field to arrange and control magnetic elements that are within the fluid. This method has a capability to adjust mixing intensity, which makes it suitable in biotechnological applications to avoid contamination (Li et al. , 2024). The involving of jet mixing was noted as a great achievement in the design of mixing tanks where high velocity jets of fluids are used to stir the tank and create turbulence that helps in the mixing process. The jet mixing system is universal, flexible and energy efficient and its working has various implementations in different areas like wastewater treatment, chemical reactor and so on (Zughbi & Rakib, 2004).
3. 2D Design Layout of Fluid Mixing Plant
The mechanical connections in the Fluid Mixing Plant are made so that the smooth functioning and seamless integration of every part. Controlled fluid flow into the Mixing Tank is made possible by the mechanical connection between Inlet Valve One and Inlet Valve Two's respective Fluid Tanks (Tank One and Tank Two) via robust pipework (Figure 1). The motor-driven mixer is housed in the mixing tank, which is where fluids one and two mix. This motor can spin and mix the fluids efficiently since it is mechanically linked to the mixer shaft. After the mixing process is finished, the combined fluid may be released by the Outlet Valve, which is linked at the bottom of the mixing tank.
To ensure durability and stop leaks, all parts are firmly fixed and linked using premium fittings. Precise monitoring and control of the whole system are made possible by the sensors, which are positioned inside the tanks and linked to the PLC Control Panel.
Two level sensors are used for detecting the level of Fluid One and Fluid two. Also, one bottom level sensor used for detecting the bottom level.
Figure 1 Modified 2D Design Layout of Fluid Mixing Plant (Red line showing electrical connection to PLC and black line is mechanical connection)
Real-time monitoring and control of fluid levels and mixing activities are ensured by the connections between the three sensors (the Low-Level Sensor, Fluid One Sensor, and Fluid Two Sensor) and the PLC Control Panel. The PLC also regulates the outlet valve and the two inlet valves, allowing for exact control of fluid entrance and exit in accordance with mixing specifications. To maintain the appropriate mixing speed and uniformity, the PLC activates and controls the Motor, which is linked to the mixer.
The PLC Control Panel serves as the central nervous system, combining sensor inputs and regulating motor, valve, and output control. This automates the whole mixing process for dependability, efficiency, and precision.
4 PLC Program for Mixing Process Control
4.1 List of Inputs/Outputs
Digital Inputs:
• Start Process Switch: I0.0
• Stop Process Switch: I0.1
• Low Level Switch: I0.2
• Level Fluid A Sensor: I0.3
• Level Fluid B Sensor: I0.4
Digital Outputs:
• Cycle ON: 1.0
• Inlet Valve 1: 3.0
• Inlet Valve 2: 4.0
• Agitator Motor: 5.0
• Outlet Valve: 6.0
4.2 Control Logic Description
Control logic description is shown in the following table:
Table 1 Control Logic Description
4.3 Ladder PLC Program
The PLC Ladder Program for the Fluid Mixing Plant automates the mixing process through a series of interconnected rungs that control the various inputs and outputs. The program begins with a latching circuit to maintain the Cycle ON state once the Start Process Switch (I0.0) is pressed. It then sequentially activates Inlet Valve 1 (3.0) and Inlet Valve 2 (4.0) based on the fluid level sensors' inputs (I0.2, I0.3, and I0.4). When both fluid levels are adequate, the Agitator Motor (5.0) is triggered, running for a set duration controlled by a timer. Finally, the Outlet Valve (6.0) is opened to discharge the mixed fluid once the mixing cycle is complete, ensuring a precise and efficient operation.
Figure 2 PLC Ladder Program created on CX- Programmer
5. Demonstration of Design Improvement
This table- 2 outlines the updated essential components used in the Fluid Mixing Plant, providing specific values for each to ensure optimal performance and compatibility within the system.
Table 2 Specification of Components for Fluid Mixing Plant
5.1 Improvements in Design
In the new design of the Fluid Mixing Plant, there are prominent areas of improvement compared to the earlier layout. In the previous design, the designed system employed the 2 Way Directional Valve which was hydraulic and the Centrifugal Pump that has high flow rate and maximum pressure ratings. Nevertheless, these components did not incorporate energy saving technologies and operating expenses were relatively high. The new design does away with these with the solenoid valves and the AC induction motor which offers a better level of control and emits less power.
Additionally, the previous system utilised a glass-lined stainless steel mixing tank with a working volume of 500 liters and conical base, yet it proves to provide some drawbacks within the mixing capability and volumetric output. The new design uses a larger 1000 liter stainless steel mixing tank, and improves the mixing speed of the vessel as well as the ability to handle greater volumes of mixed products. Also, the internal containers made from the high-density polyethylene material have now been replaced with stainless steel fluid tanks to provide enhanced durability while at the same time affording compatibility with a plethora of forms of chemicals and various types of fluids.
It is now a common practice to incorporate advanced sensors like the ultrasonic level sensors and PLC control panel hence improving the automation process greatly and increasing the efficiency of the system. These design enhancements are beneficial and effective combined that will lead to significant improvements to create a more dependable and efficient overall fluid mixing plant for the diverse industrial requirement.
6. Cost Estimation of the Machine
The cost estimation of the Fluid Mixing Plant includes the procurement of components, assembly, and installation. Below is a detailed breakdown of the costs associated with each component and other related expenses.
Table 3 Cost Details for Fluid Mixing Plant
The total estimated cost for the Fluid Mixing Plant is approximately $7,190 USD. This includes the cost of high-quality components such as solenoid valves, AC induction motor, stainless steel tanks, ultrasonic sensors, and a PLC control panel. Additionally, the costs for assembly, installation, and miscellaneous items like wiring, piping, and fittings are accounted for to ensure the complete setup and operational efficiency of the mixing plant.
7. Industrial Applications of the Fluid Mixing
The Fluid Mixing Plant is designed to meet the growing needs of various industries that require precise and efficient mixing solutions. Its applications span across:
1. Pharmaceuticals: Ensures the consistent mixing of liquid medications, syrups, and other pharmaceutical compounds, crucial for maintaining product efficacy and safety standards.
2. Chemicals: Facilitates the blending of various chemicals, ensuring homogeneity and proper reactions in products like adhesives, coatings, and cleaning agents.
3. Food and Beverages: Used for the preparation of liquid food products, beverages, and dairy, ensuring uniform taste and quality across batches.
4. Wastewater Treatment: Enhances the mixing of chemicals and biological agents in wastewater treatment processes, improving the efficiency of contaminant removal and treatment cycles.
5. Cosmetics: Supports the production of lotions, creams, and other cosmetic products, ensuring a consistent texture and quality.
6. Paints and Coatings: Enables the mixing of pigments and other components to produce paints and coatings with uniform color and properties.
8. Value of the Fluid Mixing Plant for Engineering and Technology
The Fluid Mixing Plant can be to a greater extent an innovation for mixing technology of great importance to engineering and technology industries. The first of these benefits lies in the area of accuracy and reproducibility, which is increasingly important as the complexity of the tasks performed increases. Through the provision of advanced sensors and a PLC control system, the plant guarantees differently standardized blending procedures that are important in industries that value the homogeneity of products. The last but not the least, energy efficiency is also an important thing to be mentioned here. For instance, some of the power-saving elements like the solenoid valves for controlling water flow into the tank and an AC induction motor that powers the pump help in cutting costs and thereby help in the preservation of the environment. They do this in a way that ensures costs are kept to the lowest denominator while also ensuring that impacts on the environment are minimal, thus making this plant both economical and holding the best ecological value.
Due to the advanced programming functions, the PLC control system provides a effective solution to the demands of automation and control. This makes it possible to develop the best techniques of automation, where the chances of human interjection are minimized hence enhancing the level of production. It has a flexibility aspect, meaning that depending on the company’s production requirements concerning mixing, the system can be easily programmed and customized to meet those needs. This flexibility is also reflected in the modular aspects of the plant, which can be altered easily to accommodate growing demand, meaning established industries can increase their capacities without having to make radical changes or invest heavily in new technology.
Quality assurance is another factors in its production making it a worthy plant, thus the value adding process carried by the plant. Last but not the least, the use of high-quality materials like stainless steel in making tanks and mixers implies longer periods of service without much breakdown and wear. They also make for less time spent out of order and cost of operation, the Fluid Mixing Plant can be described as tough, dependable and economically efficient for the current demand engineering and more advanced technologies.
9. Safety Factor for Operation of Fluid Mixing Plant
Safety is paramount in the operation of the projected Fluid Mixing Plant, and several key factors must be considered to ensure a safe working environment for operators and prevent potential accidents or hazards. Table 4 is outlining the safety factors to be considered for the operation of the projected Fluid Mixing Plant:
Table 4 Safety Factor for Operation of Fluid Mixing Plant
10. Conclusion
In the development of the Fluid Mixing Plant project, thorough considerations were made spanning from its industrial applications to safety protocols. It has been designed in such a way as to meet the different mixing challenges in pharmaceuticals, chemicals, food and beverages, water treatment, cosmetics, and paints and coatings industries. The plant, therefore, has the potential of delivering unique solutions in mixing to enhance production standards, quality and efficiency across main areas.
In line with implementing the technological and operational aspects of the project, the issue of safety is also deemed one of the most crucial in the sphere of industry and relevant to the development of the project. Start with electrical/mechanical safety and environmental/risk assessment – all those aspects are to besafety measures are elaborated in detail. This approach also safeguards the operators, prevents risks, and protects the vicinal environment to the would-standard requirements and norms of the relevant industry. In addition, it is an indication of the importance in applying engineering and use of technology for the improvement of operational processes. Rich in the aspect of utilizing the component technologies including the PLC control system, energy motor and automated process the Fluid Mixing Plant is highly regarded as an improvement in technology of mixing industry. The characteristic of flexibility, durability, and flexibility makes them essential in the present day engineering and technology delivery system, enhancing production efficiency as well as reducing costs, while upholding sustainable production principles.
11. References
Aubin, J., & Xuereb, C. (2006). Design of multiple impeller stirred tanks for the mixing of highly viscous fluids using CFD. Chemical Engineering Science, 61(9), 2913–2920. https://doi.org/10.1016/j.ces.2005.10.075
Bowler, A. L., Bakalis, S., & Watson, N. J. (2020). Monitoring Mixing Processes Using Ultrasonic Sensors and Machine Learning. Sensors, 20(7), 1813. https://doi.org/10.3390/s20071813
fpt. (2023). Industrial Mixer and its mixing technology. Kiron Food Processing Technologies LLP. https://www.fptindia.com/blog/industrial-mixer
Hoo, D. Y., Low, Z. L., Low, D. Y. S., Tang, S. Y., Manickam, S., Tan, K. W., & Ban, Z. H. (2022). Ultrasonic cavitation: An effective cleaner and greener intensification technology in the extraction and surface modification of nanocellulose. Ultrasonics Sonochemistry, 90, 106176. https://doi.org/10.1016/j.ultsonch.2022.106176
Ian, & Changying Ji . (2018). A Study of the Mixing Performance of Different Impeller Designs in Stirred Vessels Using Computational Fluid Dynamics. Designs, 2(1), 10. https://doi.org/10.3390/designs2010010
iqsdirectory. (2022). Agitators: Parts, Types, Flow Patterns, and Configurations. Www.iqsdirectory.com. https://www.iqsdirectory.com/articles/mixer/agitators.html
Li, J., Su, K., Liu, H., & Zou, Y. (2024). Recent Advances in Magnetically Actuated Droplet Manipulation for Biomedical Applications. Magnetochemistry, 10(4), 28. https://doi.org/10.3390/magnetochemistry10040028
Singla, M., & Sit, N. (2021). Application of ultrasound in combination with other technologies in food processing: A review. Ultrasonics Sonochemistry, 73, 105506. https://doi.org/10.1016/j.ultsonch.2021.105506
Ye, L. (2024). Design of PLC Electrical Control System. Journal of Theory and Practice of Engineering Science, 4(03), 134–162. https://doi.org/10.53469/jtpes.2024.04(03).13
Zughbi, H. D., & Rakib, M. A. (2004). Mixing in a fluid jet agitated tank: effects of jet angle and elevation and number of jets. Chemical Engineering Science, 59(4), 829–842. https://doi.org/10.1016/j.ces.2003.09.044