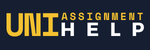
EMS5RCE Risk Engineering Report 2 Sample
1 Outline
You have been tasked to evaluate the risks associated with moving from a traditional construction method for constructing concrete formwork (such as precast), to an advanced method that will be designed to take advantage of additive and/or automated and digital techniques.
Firstly, draw on your engineering background to gain an overview of the current construction methods and their respective times. Obviously, this information may not be readily available, therefore, you may be required to make some assumptions – but use your engineering judgements to make sure these are justified.
Then, select an appropriate advanced / alternative method for your project. It could also be a future construction method that is yet to be commercialised. Remember, this subject is about risk engineering, and this report does not require a full technical evaluation. The next stage will be to implement a risk management process based on the ISO31000 and the content of this course. Some things to think about would include:
Risks and opportunities
Hazards
Safe design principles
The risk management process
o Risk identification
o Risk analysis
o Risk evaluation
o Risk treatment
o Risk monitoring and review
Techniques and tools used for planning and probabilistic analysis
o CPM
o PERT
o Monte Carlo
Summary
o Conclusions and lessons learnt
o Recommendations
o Future research
Go through the step-by-step process with your team, brainstorm what the different risks for you company and project are, where they are coming from, are they internal or external, what category, etc. Set-up a risk matrix and score the various risks.
With regard to the techniques and tools you will use for planning and probabilistic analysis you may wish to compare different methods. For instance, one could compare the use of PERT calculations to a Monte Carlo simulation?
You will need to include at least one network diagram – preferably two. One could be either specific to an assembly process (such as print part ? machine part ? assemble part etc.).
The other could be related to your company as a whole, i.e., buy raw materials ? manufacture part ? package and store ? ship part/component to customer etc. In each case there are risks involved and they can be assigned times, or costs or both.
How can digital design/construction be of use when implementing and monitoring risks? Could you think of a feedback loop for data along the path? These are some of the questions you should cover in your report.
2 Instructions
The Assignment can be laid out as follows:
Use the font sizes specified in the individual assignment.
Font can be Timed New Roman, Calibri or similar.
Use spell check and read your assignment before submitting.
Reference figures and other sources of information. Use a referencing tool such as Zotero https://www.zotero.org/
Use the numeric IEEE style type.
2,000 words per person! Be concise!
To ensure your submission fits the page/word count ranges, make certain to count words in the body using your word processor and then add in the equivalent word counts for your tables and images. References do not count towards the wordcount. Figures and tables are counted by the amount of words they replace. Make sure you include only highly relevant images and remove non-essential images to help your manuscript be more reader-friendly while fitting within the page/word limits.
Use the same layout (font sizes, section headings etc.) that was provided for the first assignment. The body of the paper usually contain the following sections:
La Trobe Cover Sheet
Title
Authors first and last (given and family) names and student numbers and e-mail address
Summary (400 words maximum, no graphics)
Introduction
Body
Conclusions/Summary
Acknowledgements (if any)
References
Systéme International (SI) units are to be used. Non-SI measurements can be included, but they should follow the SI measurement in parentheses. An example is 2.54 cm (1.00 inch).
Solution
Summary
The dedication of innovation and sustainability can be observed in the construction industry's continually movement towards new technologies, such as the 3D printing of concrete formwork. Though dependable, conventional methods such as precast concrete formwork have drawbacks in terms of cost, time, and design flexibility. University Assignment Help, Significant benefits from 3D printing include the capacity to create complicated structures with precision, lower labor intensity, enhanced sustainability, and the potential to completely transform the construction industry. This shift calls for strict risk management in accordance with ISO 31000 guidelines, and the choice of methods must take into account a number of important criteria, including cost, sustainability concerns, project needs, and technical viability.
Introduction
The construction sector is undergoing an extensive transition towards sophisticated building techniques that leverage additive, automated, and digital technology as a result of a desire for innovation and sustainability [1]. Conventional building techniques, such as precast concrete formwork, have long served as the foundation of the construction sector. These techniques are efficient, but they frequently have drawbacks in terms of speed, cost-effectiveness, and design flexibility [2]. 3D printing has emerged as a competitive substitute in the search for more effective, eco-friendly, and adaptable building methods.
The process of designing and constructing formwork for concrete buildings is revolutionized by 3D printing, commonly referred to as additive manufacturing [3]. Using large-scale 3D printers, this technique creates complex, personalized formwork constructions layer by layer. The benefits are numerous and include creative flexibility, lower labor intensity, increased sustainability, and precise construction of intricate geometries. This strategy might completely transform the building sector by providing a link between innovative architectural concepts and successful, economical implementation.
Current Construction Methods: Overview and Timelines
A popular and established technique for building a variety of concrete structures, such as walls, columns, beams, and slabs, is precast concrete formwork. This method's main feature is that formwork components are made in a manufacturing facility. After being ready, the formwork components are brought to the building site and put together to make the moulds needed to pour concrete [2]. After that, the concrete is poured into these prefabricated formwork structures, ensuring consistency and homogeneity in the finished result.
Timelines for Precast Concrete Formwork
Precast concrete formwork construction schedules can differ depending on a number of factors, such as the complexity of the project, the design of the formwork, the efficiency of manufacture, and the logistics of transportation [4]. However, Figure 1 provides the following generalized schedule for a typical precast concrete formwork project:
• Creating the formwork design to satisfy structural requirements and creating project specifications are the main tasks of the first Design and Planning Phase (2-4 weeks).
• After that, the formwork components are fabricated at the precast yard during the Manufacturing Phase, which lasts for 4-6 weeks.
• After the formwork components are carried to the building site, unloading and site preparation take place over the course of one to two weeks.
• After that, formwork assembly takes two to four weeks, depending on the size and complexity of the design. This process creates moulds for the pouring of concrete.
• The size, volume, and curing time of the concrete pours determine how long the Concrete Pouring and Curing phase takes.
• The formwork is disassembled and removed during the post-curing, stripping and demobilisation phase (1-2 weeks), and
• the concrete structures are ultimately checked to make sure they satisfy the required specifications during the finishing and quality control phase (2-4 weeks).
Figure 1 Generalized timeline of precast concrete formwork construction
Assumptions and Justification
When talking about precast concrete formwork timescales, these might differ significantly based on the particular project, regional laws, and other outside influences. It is essential to carry out a thorough project-specific study, taking into account factors like project scale, formwork complexity, labour efficiency, and environmental circumstances, in order to produce a more accurate evaluation of timetables for a particular task.
Factors Influencing the Selection of Advance Method
It demands analysis of the various factors as listed below.
1. Project Requirements: The particular requirements of the project should be the primary factor taken into account while choosing an advanced building approach. For instance, a high-rise urban building project would need for a technique that maximises accuracy and speed.
2. Technological Feasibility: When making decisions, innovative building technologies' maturity and accessibility are crucial factors.
3. Cost and Budget: The financial implications of adopting an advanced construction method are significant. Additionally, the long-term cost considerations, including maintenance and training, need to be assessed.
4. Time Efficiency: By shortening construction times and speeding up project completion, the improved approach should enhance project schedules.
5. Sustainability and Environmental Impact: The method should align with eco-friendly practices, potentially reducing waste and energy consumption.
Risk Management Process: Applying ISO 31000 Principles
Effective risk management is crucial when switching from conventional building techniques to cutting-edge substitutes like 3D printing concrete formwork. A thorough framework for risk management is offered by the ISO 31000 standard, which emphasises the necessity of using a methodical and organised approach to recognise, assess, evaluate, manage, and keep an eye on risks throughout a project [5].
Risk Identification
The first step in the risk management process is the identification of potential risks. For a construction project embracing advanced methods like 3D printing, it is essential to consider both internal and external sources of risk. This involves:
• Internal Risks: These are risks inherent to the project and the organization undertaking it. They may include technological challenges, lack of expertise, or budget constraints.
• External Risks: External risks can emanate from factors beyond the project's control, such as changes in regulations, market dynamics, or environmental factors.
Risk Analysis
This risk analysis uses a low, moderate, and high scale to evaluate likelihood and a low, mid, and high scale to evaluate effect. Project managers are able to create suitable risk mitigation measures and prioritise hazards for additional analysis thanks to this evaluation. High probability and high impact risks are usually handled more quickly and carefully to reduce any possible negative consequences they may have on the project.
Risk Evaluation
We constructed a risk matrix for the likelihood and effect of each identified risk in order to conduct a risk evaluation using ISO 31000. The numerical values will aid in the evaluation and ranking of these hazards. This is a tabular summary of the risk assessment.
Table 1 Risk Matrix
Risk Treatment
After conducting a comprehensive risk analysis using ISO 31000 and evaluating the likelihood and impact of each identified risk, the next step in the risk management process is developing and implementing suitable risk treatment measures.
Table 2 Risk Treatment
Risk Monitoring
Managing risks effectively is a continuous effort. A key component of the ISO 31000 system is the ongoing monitoring and assessment of risks. Regular monitoring guarantees that risk remedies are effective and that new hazards are quickly detected and handled in building projects that use sophisticated technology. This stage entails monitoring important risk indicators, making necessary adjustments to risk treatment strategies, and fostering open dialogue among project stakeholders.
Comparative Analysis of Project Planning and Probabilistic Analysis Techniques
The planning and probabilistic analysis techniques—CPM, PERT, and Monte Carlo simulation—are summarised in following tabular comparison, together with their applications, benefits, and drawbacks. It enables project managers to decide with confidence which approach best fits the unique requirements and complexity of their building project.
Table 3 Comparative Analysis of Project Planning and Probabilistic Analysis Techniques
Network Diagrams
We will explore two types of network diagrams: assembly process-specific and company-wide diagrams, and discuss the assignment of times and costs to identified risks.
Assembly Process-Specific Network Diagram
This is a simplified network diagram showing how a 3D printing building method is assembled:
Figure 2 Assembly Process-Specific Network Diagram (3D Printing Construction)
Company-Wide Network Diagram
An overall picture of the construction process, from locating raw materials to delivering the finished product to the client, is shown by the company-wide network diagram. This schematic represents every stage of the undertaking, encompassing acquisition, production, assembling, and transportation
Figure 3 Company-Wide Network Diagram
Role of Digital Design/Construction in Risk Management
One of the most important ways to reduce the hazards associated with cutting-edge building techniques like 3D printing concrete formwork is through the integration of digital design and construction technology, such as Building Information Modelling (BIM) and construction management software [6]. Construction management software allows for effective communication, resource allocation, and real-time project monitoring, while BIM allows for the visual representation of complicated projects, clash detection, design alternatives assessment, and real-time cost calculation. A proactive and constantly evolving approach to risk management in the construction sector is further promoted by creating a feedback loop for data, which guarantees that insights from the design, construction, and monitoring phases continuously improve risk reduction measures.
Conclusion
In summary, the use of cutting-edge building techniques like 3D printing concrete formwork represents a revolutionary advancement. It necessitates a proactive approach to risk management that makes use of advanced planning and analytical methods, ISO 31000 standards, and the potential of digital design and construction. The construction sector may achieve increased efficiency, sustainability, and resilience in the face of changing problems by adopting these practises and keeping up with innovation.
Reference
[1] A. O. Olanipekun and M. Sutrisna, “Facilitating Digital Transformation in Construction—A Systematic Review of the Current State of the Art,” Frontiers in Built Environment, vol. 7, Jul. 2021, doi: https://doi.org/10.3389/fbuil.2021.660758.
[2] D. W. M. Chan and A. P. C. Chan, “Public Housing Construction in Hong Kong: A Review of its Design and Construction Innovations,” Architectural Science Review, vol. 45, no. 4, pp. 349–359, Dec. 2002, doi: https://doi.org/10.1080/00038628.2002.9696950.
[3] T. D. Ngo, A. Kashani, G. Imbalzano, K. T. Q. Nguyen, and D. Hui, “Additive manufacturing (3D printing): A review of materials, methods, applications and challenges,” Composites Part B: Engineering, vol. 143, pp. 172–196, Jun. 2018, doi: https://doi.org/10.1016/j.compositesb.2018.02.012.
[4] Jonny Nilimaa, Yaser Gamil, and Vasiola Zhaka, “Formwork Engineering for Sustainable Concrete Construction,” CivilEng, vol. 4, no. 4, pp. 1098–1120, Oct. 2023, doi: https://doi.org/10.3390/civileng4040060.
[5] C. Lalonde and O. Boiral, “Managing risks through ISO 31000: A critical analysis,” Risk Management, vol. 14, no. 4, pp. 272–300, Nov. 2012, doi: https://doi.org/10.1057/rm.2012.9.
[6] J. Teizer et al., “BIM for 3D Printing in Construction,” Building Information Modeling, pp. 421–446, 2018, doi: https://doi.org/10.1007/978-3-319-92862-3_26.