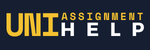
ADM80001 Nanofabrication Technologies Report Sample
Assignment Brief
Major Project Guidelines & Structure
Report Outline:
The Major Project Report should be ~ 20-30 pages long with text, tables and figures. The report should contain significant research of recent scientific and technical literature relating to the topic you chose. The aim of the project is to use the knowledge you have gained in nanofabrication towards a potential manufacturing application. Examples of possible projects are listed below.
Please note the Project Topic must be significantly different from your topic in Assignment 1.
Guidelines:
Details below outline a suggested layout which can be used as a guide to prepare your Project.
• Title Page – This page should contain the project title and any contributing authors
o Conveys the area and scope of the project
o Short and concise, but descriptive
• Abstract – Contains a summary of the report
o Used to help the reader to quickly ascertain to purpose of the report
o Approx. 200-300 words
• Table of contents – Indicates the page numbers of different sections
• Introduction – Outlines the underlying concepts needed to discuss the project
o Introduction and interpretation of any theory
o Approx. 800-1000 words
• Main body of project – Presents key ideas of the topic in a descriptive and informative way
o Provides all the details of your findings with reference to the aims of your report
o Broken down into sections and sub-sections (if applicable)
o Provides a detailed literature review relevant to your chosen topic.
o Presents a comprehensive discussion on the nanofabrication technique(s) and the nano characterisation techniques used to your potential manufacturing application
o Approx. 20 pages
• Conclusions – Draws conclusions from the information and ideas presented
o Provides a concise summary of your main arguments for the use of your topic in emerging or potential manufacturing applications
o Approx. 300-400 words
• References – Lists the resources used to construct the project report
• Appendices (if any)
Project report Assessment:
• Quality of scientific research
o Use peer reviewed journal articles, review articles, book chapters, patents etc.
o Web pages can be used sparingly but should be from credible sources i.e. educational (.edu) or governmental (.gov) sites.
• Quality of scientific writing
o Clear and simple language should be used: avoid vague or complicated sentences
o Statements and ideas should be supported by appropriate data and evidence
o Key ideas and themes should be presented in a logical manner by dividing text into sections with clear descriptive headings
• Project length, number and quality of tables and figures
o Approx. 20-30 pages
o 10-15 tables and/or figures
o All tables and figures should be introduced in-text and be referenced properly using a consistent style.
• Quantity and consistency of references
o 20-30 references
o Consistent style used (Harvard or similar should be used)
• Turnitin similarity score
Solution
Introduction
Research Background
The problem of corrosion is one of the major issues to be addressed in a variety of industries, such as automotive, aerospace, marine, infrastructure, and electronics. It results in material deterioration, structural failures, higher maintenance costs, and decreased safety. The traditional methods of corrosion protection, for example, painting and coatings, are not always the practical and of long-term ways, especially in areas with permanent extremely high or low temperatures, humidity, and chemicals. The emergence of nanotechnology has transformed the area of corrosion protection with nanocoatings as an alternative solution. Nanocoatings are nanoscaled materials designed to create a protective layer on the surface of the substrate (Nanografi Nano Technology, 2024). They provide numerous benefits compared to the conventional coatings such as better corrosion resistance, better mechanical properties, improved adhesion, and longer life for university assignment help.
Development of nanocoatings for corrosion resistance is provided by nanomaterial synthesis improvements, surface modification techniques, and characterization methods. Nano elements, e.g. graphene, carbon nanotubes, metal oxides and polymers which have their own special features at the nanoscale work well enough for use in many corrosion control applications. With this progress in coatings formulation as well as application processes, nano coating has been designed with the ability to possess custom features arranged to cater for the demand prevailing in each industry (Nhiem et al., 2023).
Research Aim
The aim of this project is to investigate and develop corrosion-resistant nanocoatings as an effective solution for combating corrosion in various industrial applications.
Research Objectives
• To analyse the nanomaterials with corrosion resistant properties and characteristics.
• To conduct research on the techniques to assess the performance of the nanocoating.
• To develop optimised formulations of the nanocoating by using nanomaterials, binders, and additives to ensure enhanced adhesion, durability, and corrosion resistance.
• To examine the scalability of the envisioned nanocoating procedure and size up its value in trade.
Project Scope
This project is aimed at inventing and implementing of corrosion resistant Nanocoating in industrial sphere. The focus is on determining the nanoparticles with desired characteristics, constructing a formulation, laboratory testing procedures and determining if it can be scaled. The aim of the project is the investigation of the specs of numerous nanostructure materials namely graphene, carbon nanotubes, metal oxides, and polymers in relation to the corrosion inhibition propensity. Formulation development proceeds from defining of the optimum nano-coating composition with the combination of certain nanomaterial with binders and additives. Such laboratory testing is expected to give an associated amount of data on how the constructed nanocoatings will react to such environmental conditions as salt spray and electrochemical testing. In addition, the project will examine scalability of the nanocoating process and investigate its commercial viability covering among others areas like affordability, application convenience and suitability in connection with the current production methods.
Literature Review
Analysis of Nanomaterials for Corrosion Resistance
According to Farag, (2020), Nanoparticles are the main building block in the fabrication of corrosion-resistant nanocoatings because of their excellent attributes of magnetism at the nanoscale. Among the several nanomaterials studied, graphene seems to be outstanding because of its particularly high mechanical strength, along with an impressive surface area, and an impermeability to both gases and liquids. It has been proven that the application of graphene-based nanocoatings provides a superior level of protection from corrosion as these coatings act as a barrier against the harmful corrosives and also offer electron transfer that hinder oxidation reactions.
According to Rooy et al., (2021), Carbon nanotubes (CNTs), being on the forefront due to their high aspect ratio, electrical conductivity, and chemical stability, is receiving a lot of attentions. The interaction of the CNT nanocoatings with substrates, either physical or electrochemical, leads to the inhibition of corrosion, being more effective than traditional barrier coatings. Metallic oxides such as zinc oxide (ZnO) and titanium dioxide (TiO2), the creation of the nanostructures they can be done when a tunable morphology and surface chemistry can be achieved. Although these nanomaterials behave passively by placing themselves on the surfaces, they also function as sacrificial anodes which inhibit the diffusion of corrosive species and metal oxidation.
Allowing polymers that are functionalized with nanoparticles to offer one more alternative to avoid corrosion by integrating the inherent properties of polymers with those of the nanomaterials. The blending of nanoparticles with the nanocomposite results in superior mechanical strength, flexibility, and self-adherence that renders them suitable for use in multiple applications that require corrosion resistance (Huang et al., 2020).
Different synthesis methods employed to fabricate Nanocoatings
According to Afolalu et al., (2023), Various methods employed in the synthesis determine the structure, composition, and properties of final coating. Of all these methods, chemical vapor deposition (CVD) is the most effective is producing uniform, conformal coatings with a high level of control over the thickness and composition. CVD is the chemical reaction of precursor gases on the surface of a substrate to form thin films of selected nanomaterials that include metals, metal oxides, and carbon-based materials. another step is to manufacture and use Sol-gel which offers an approach for nanocoating by hydrolysing and condensing metal alkoxides on order to form a gel. This can be deposited substrates through dipping, spin-coating, or spraying (Jin et al., 2023). Coatings derived from sol-gel have excellent adhesion, homogeneity, and chemical stability, which makes them suitable for anti-corrosive applications.
Electrochemical deposition (ECD) allows the regulated deposit of nanocoatings by the use of electric current to increase or reduce metal ions in a solution onto a conductive substrate. ECD produces closely packed, uniform coatings of adjustable thickness and composition that provide the desired corrosion protection properties. Sputtering is one of the physical vapor deposition (PVD) techniques where the nanomaterial is physically vaporized followed by condensation onto a substrate and thin film formation# alternatives where sputtering is used as an example of PVD technique (Yasin et al., 2020). PVD approaches have a great deal of control over the film thickness, density, and crystallinity, which means that the nanocoatings produced in these ways are of high purity and uniformity.
Performance Evaluation Techniques
Mogra et al., (2020) states that the methodologies of performance evaluation is extremely important part of the process in which nanocoatings is being measured to check how good they are in provides anti corrosion properties. Several ways of analyzing different coating properties are employed, e.g. adhesion, flash point, strength, corrosion resistance, and surface structure. The most highly-applied corrosion test, the saline spray testing, which accelerates the corrosion process, is done by spraying salty water mist onto the coated samples to mimic unfavorable conditions. This method provides the assessment of the coating's reliability in the corrosive media so that this information could be used as an evaluation of stability and efficiency of the anti-corrosive coatings.
According to Magar et al. (2021), EIS (Electrochemical Impedance Spectroscopy) has proved its capability of finding the time-varying resistive responses that are in the form of a complex number and characterize the electric/electrochemical behavior of coatings. EIS Data are utilized to analyze coating integrity, corrosion kinetic and the ion mobility processes maximum data in which the determination of corrosion resistance and barrier properties are achieved. Scanning electron microscopy (SEM) and atomic force microscopy (AFM) are the typical two imaging techniques that one can employ for a detailed study of the surface morphology and topography of the substrate coatings surface analysis. SEM shows very detailed images of the coatings which are defect-free and well adjusted and, on the other hand, AFM demonstrates how the films roughness levels are depending on how they are adjusted. X-ray photoelectron spectroscopy (XPS) for probing the elemental composition and chemical bond conditions in the surface of coatings. XPS analysis includes identification of the coating constituents, oxidation stages and pollutants. This enables referencing to the processes undertaken that are specific for the corrosion prevention (Hamada et al., 2023).
Enhancement Strategies for Nanocoatings
Xi et al. (2020) considered the strengths of the nanocoating design to be improvable from the standpoints of their lifespan and operation though the means of improving the coatings. Multiple improvements were introduced, including coatings modifying the surface, using nanofillers, composite coating along with multilayered structures. Surface functionalization can be defined as the process which the chemical surface coating modification are implemented to the material by means of adhesion and resistance from corrosion as well as barrier properties. For example, several groups of chemists like silanes, phosphates and fluoropolymers would be utilized to reinforce the adherence to substrate and stop corrosion initiation and propagation (Zhou et al., 2022).
Nano-additives including nanoparticles, nanotubes, and nanofibers are used for the coating formulation to improve mechanical behaviors, barrier properties, and corrosion resistance. Nano-additives detain aggressive particles by creating a physical barrier, prevent diffusion paths and create a sacrificial surface to protect the substrate. Combining nanomaterials with primordial coating materials helps to form coatings that are of a composite type due to synergistic properties. The composite coatings which results from the combination of different materials, i.e, polymers, ceramics, and metals, have the mechanical strength enhanced, chemical resistance and corrosion protection improved (Zhou et al., 2022).
The structure implementing multi-layered system is achieved through sequentially depositing disparate materials to yield one coating with multifunctional properties. Multilayered nanocoatings due to the property of enhancing of corrosion resistance, and adhesion qualities, and barrier function of nanocoatings, all are acknowledged to be contributed with the layer-to-layer interface and, the diffusion level of corrosive species.
References
Afolalu, S.A., Ikumapayi, O.M., Ogedengbe, T.S., Kayode, J.F., Ogundipe, A.T. and Jen, T.C., 2023. A review on emerging trends in the scientific application of nano-coatings and nanoparticle synthesis. Materials Today: Proceedings.
Farag, A.A., 2020. Applications of nanomaterials in corrosion protection coatings and inhibitors. Corrosion Reviews, 38(1), pp.67-86.
Hamada, M.A., Khalil, H., Abou Al-Sood, M.M. and Sharshir, S.W., 2023. An experimental investigation of nanofluid, nanocoating, and energy storage materials on the performance of parabolic trough collector. Applied Thermal Engineering, 219, p.119450.
Huang, H., Sheng, X., Tian, Y., Zhang, L., Chen, Y. and Zhang, X., 2020. Two-dimensional nanomaterials for anticorrosive polymeric coatings: a review. Industrial & Engineering Chemistry Research, 59(35), pp.15424-15446.
Jin, H., Ji, R., Sun, H., Wang, K., Li, X., Liu, S., Wang, L., Zhao, L., Ma, C., Cai, B. and Liu, Y., 2023. Preparation of tubing inner surface reinforced layer by inert anode assisted jet electrodeposition. Tribology International, 187, p.108699.
Magar, H.S., Hassan, R.Y. and Mulchandani, A., 2021. Electrochemical impedance spectroscopy (EIS): Principles, construction, and biosensing applications. Sensors, 21(19), p.6578.
Mogra, A., Pandey, P.K. and Gupta, K.K., 2020. Enhancement of boiling heat transfer performance using nano coating-a review. Journal Of Advanced Research In Fluid Mechanics And Thermal Sciences, 71(1), pp.100-116.
Nanografi Nano Technology. (2024). Anti-Corrosive Nanocoatings. [online] Available at: https://nanografi.com/blog/anticorrosive-nanocoatings/ [Accessed 6 May 2024].
Nhiem, L., Yen, T. and Hieu, N. (2023). Nanocoating toward anti?corrosion: A review. Vietnam Journal of Chemistry, [online] 61(3), pp.284–293. doi:https://doi.org/10.1002/vjch.202300025.
Rooby, D.R., Kumar, T.N., Harilal, M., Sofia, S., George, R.P. and Philip, J., 2021. Enhanced corrosion protection of reinforcement steel with nanomaterial incorporated fly ash based cementitious coating. Construction and Building Materials, 275, p.122130.
Xi, R., Wang, Y., Li, X., Zhang, X. and Du, X., 2020. A facile strategy to form three-dimensional network structure for mechanically robust superhydrophobic nanocoatings with enhanced transmittance. Journal of colloid and interface science, 563, pp.42-53.
Yasin, G., Arif, M., Mehtab, T., Shakeel, M., Khan, M.A. and Khan, W.Q., 2020. Metallic nanocomposite coatings. In Corrosion protection at the nanoscale (pp. 245-274). Elsevier.
Zhou, Q., Wu, T., Bai, Z., Hong, G., Bian, J., Xie, H. and Chen, C., 2022. A silane-based coupling strategy for enhancing the mechanical properties of proanthocyanidin nanocoatings on Ti dental implants. Applied Surface Science, 602, p.154400.